Discover our Product
Our proprietary technology guarantees that Recharge protection systems maximise the life cycle of bogies, reduce maintenance costs, and deliver competitive advantage.
DO YOU WANT TO KNOW HOW?
The Recharge solution replaces coating and
paint-based protection systems that make it difficult to inspect and maintain
the bogie. Instead, we offer a removable, modular, customisable, repairable,
and reusable protection solution made from recycled composite materials.
Cellular structures with auxetic behaviour give our protection systems
their technological edge.
Our wheelset shock absorber* solution can absorb 9 times the impact energy at low speed, up to 120 km/h. Therefore, our solution is suitable for high-speed trains up to 360 km/h.
* Impact validation with 120° conical tip as required by regulation.
Improves impact energy absorption by up to 40%
DO YOU WANT TO LEARN ABOUT OUR PROCESS?
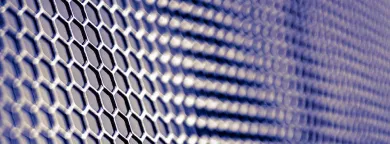
Materials
Recent advances in railway structures demand lightweight designs to
reduce energy consumption and track load. Fibre Reinforced Polymers
(FRP) are lightweight, strong, rigid, and corrosion resistant, and
are widely employed in the rail industry. Fibre-reinforced
thermoplastic materials (FRTP) are also emerging as an attractive
proposition for structural components because of their fast
processing, recyclability, and energy absorption capacity under
impact.
Our protection systems are manufactured from polyamides and polypropylenes
reinforced with glass fibres in collaboration with leading raw material
suppliers. All products are fully compliant with fire regulation EN-45545-2.
Complex cores and cellular structures
Composite materials can deliver the lightweight and strong structures the transport industry demands. The critical component of these materials is the core, as this distributes loads and improves strength and stiffness, ultimately achieving an optimal balance between weight and performance. Recharge supplies hexagonal and corrugated cores and cellular structures, with a focus on re-entrant (auxetic) or bio-inspired (trabecular) structures because of their excellent impact properties.
Trabecular (Beetle): Structures with higher impact resistance than conventional honeycomb structures.
Auxetics (Negative Poisson Ratio): Structures which densify under compression load, improving energy absorption capacity.
Manufacturing Processes
Selecting the most suitable technology for manufacturing composite parts
depends on many factors such as production volume, the geometrical
complexity of the component, and the required mechanical properties.
Recharge combines conventional polymer processing
technologies such as extrusion, thermoforming, thermoforming extrusion, thermoforming,
GMT, and injection moulding to manufacture our products.